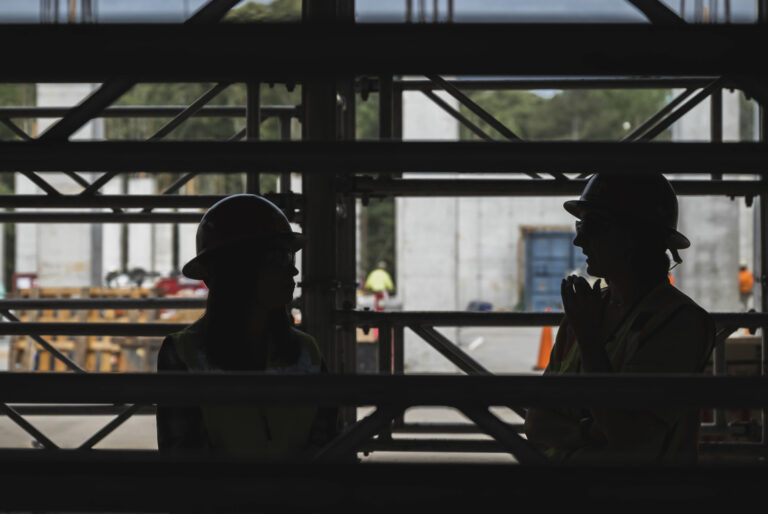
The difference
We’re a blue collar company with white glove service
You have high expectations. So do we. That’s why it’s not just a project when you’re working with our team–it’s a partnership where iron sharpens iron.
Excelling through self-perform
Leaning on the skills of our own teams allows us to control the construction schedule and save our clients time and money.
See us in action
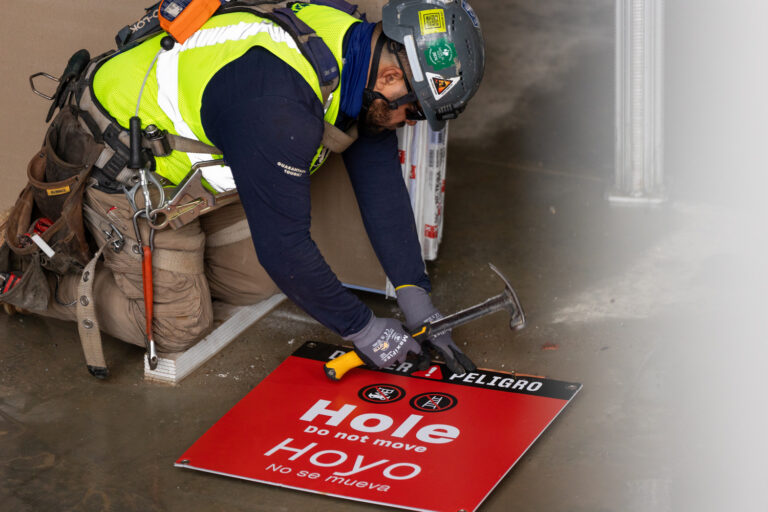
Safety
Hope is not a strategy
Our safety philosophy boils down to one simple principle: People come first, no exceptions. It’s at the forefront of every plan, decision, and action we take. We’re responsible for everyone on our projects, and we take that seriously.
Preconstruction isn’t a transactional relationship where the client sends us the drawings and we tell them how much it’s going to cost. When we’re involved early in the process, we can help clients understand all the different aspects of the design and help them maximize their budget and stay on schedule by providing options and solutions.
Preconstruction
Ahead of the curve
Pricing is just the beginning
We go beyond the industry standard and offer solutions—not just an estimate. Whatever your project goals, our services and skills will deliver a complete plan ready to execute in the field.
True partners you can trust
Every project is a team effort from the beginning. We collaborate with design teams and enlist expertise from all corners of our company to offer you accurate feedback and innovative ideas that add value.
Real builders, real results
Precision comes from more than the tools we use—our greatest assets are the people using them. With decades of hands-on construction experience, our team will provide insights that prevent unwanted surprises once the shovel hits the dirt.
Services and delivery methods
In the intricate world of construction, your project deserves a general contractor with the flexibility and expertise to make your dreams a reality.
Innovation
We don’t just come to work, we come to think.
We’re constantly exploring new ways to bring value to our clients and pushing for 1% better every day.