- Healthcare
The large and small of offsite prefabrication
July 21, 2022
Every so often, a significant new technology emerges and changes the construction industry for the better. And prefabrication has done just that for several years by allowing project teams to build various components offsite at a safer and more efficient pace, typically in environments that are more attractive to workers and less prone to weather impacts.
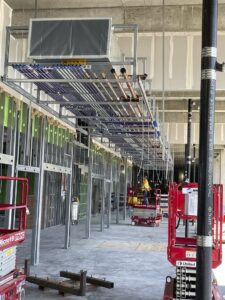
When prefabrication first gained traction, the focus was on bigger pieces. Components such as bathroom pods, mechanical racks, and modular headwalls became useful options for projects that depend on tight schedules and reduced costs, particularly for healthcare and hospitality clients. As prefabrication has increased in popularity, though, the construction industry’s interest in prefabrication now includes smaller components that might not otherwise be considered.
“Even if it’s just precut and kitted materials, that is an innovative way for our trades to make sure they have all the necessary materials for a certain space,” said Director of Lean Construction Katie Wells. “You may not be preassembling the whole system, but you’re looking at how to be the most efficient.”
For example, smaller prefabricated components are common among electrical trades. At an offsite facility, workers will implement processes like kitting boxes and precutting conduit before color-coding these items based on where they’ll be installed. Once these boxes are assembled and labeled, they can be transported to their ultimate destination in bulk, saving onsite workers time and increasing their productivity.
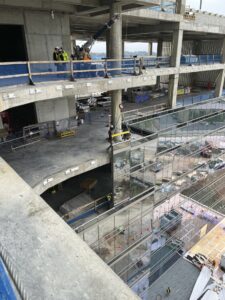
On the Children’s Healthcare of Atlanta Arthur M. Blank Hospital jobsite, prefabrication is being implemented to construct several elements like multi-trade racks, light fixtures, and exterior wall systems.
“Offsite prefabrication offers the opportunity for our trade contractors to increase the efficiency of their skilled workforce by having them work in a more productive environment,” said Operations Manager David Hajjar. “That environment not only produces finished product faster, but also improves quality and safety metrics as workers can focus solely on the task in front of them.”
That controlled environment has been especially helpful during the COVID-19 pandemic, and the prevalence of prefabrication is on the rise as a result. As protective protocols have become standard, project teams have shifted some processes to offsite locations. Creating a workflow that requires fewer workers also helps mitigate the ongoing industry-wide labor shortage.
At Inglett & Stubbs, an electrical contractor on the Arthur M. Blank Hospital project, teams constantly search for ways to improve workflow through prefabrication, no matter the size of the materials. Their facility includes 75,000 square feet of space with between 75 and 125 people working at any given time, and it’s located within 10 miles of the jobsite.
“We prefab as much of this stuff as we possibly can,” said Scott McConnell, QA/QC foreman at Inglett & Stubbs. “We get challenged to come up with something better to make our work more efficient. The Inglett & Stubbs prefab team give us the freedom to fail before we figure out a better way. You never know what somebody’s going to come up with.”
Though prefabrication has been a prominent fixture of the construction industry in recent years, it’s not a blanket solution for every project. Brasfield & Gorrie crafts a custom approach for each project, and we always consider how prefabrication can help us and our clients in terms of scheduling, efficiency, and quality.
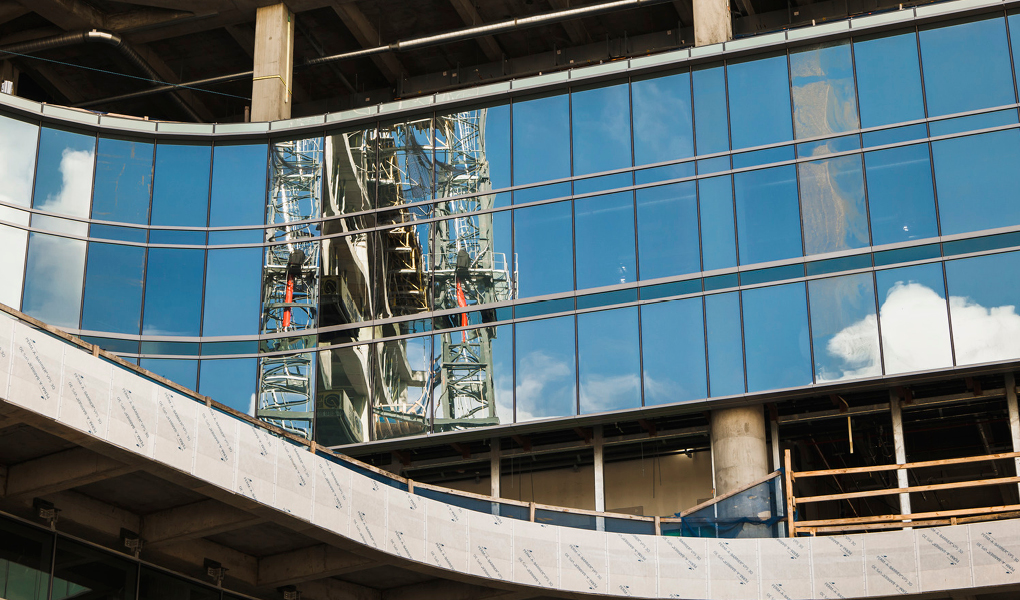
Related